How Do PET Plastic Preform Molds Work?
What Role Do PET Preform Molds Play in the Plastic Injection Molding Process?
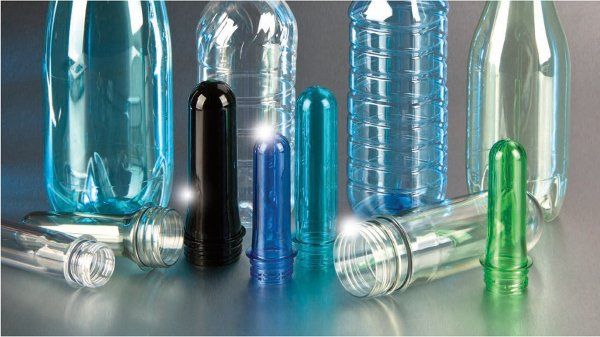
When it comes to modern packaging, PET (polyethylene terephthalate) plastic preforms have emerged as a revolutionary solution for creating containers that are both durable and lightweight. These preforms are the early stage of PET plastic bottles before they undergo the blow molding process. But the key to the seamless production of these preforms lies in the PET plastic preform molds.
Understanding PET Plastic Preforms
Before delving into the mechanics of the mold, let's take a moment to cover the PET plastic preforms themselves. These preforms, which are made of PET resin, are created through the injection molding process and resemble miniature bottles, complete with threaded necks and closed bottoms. These preforms are heated and stretched during the blow molding process to create the final PET bottles.
The Role of PET Plastic Preform Molds
The PET plasticc preform molds serve as the backbone of the entire preform production process. These molds are engineered with precision to produce identical preforms that meet industry standards in terms of weight, dimensions, and design. By design, these molds can handle a wide range of preform sizes and shapes.
The Injection Molding Process
Mold Cavity Creation: The process begins with the design of a mold cavity, which represents the desired shape of the PET preform. These cavities are typically made from high-grade steel to withstand the stress and high temperatures of the injection molding process.
Plastic Resin Injection: Small pellets of PET resin are fed into the injection molding machine's hopper. The pellets are heated and melted, forming a molten plastic material.
Injection into the Mold: The molten plastic is then injected into the mold cavity under high pressure. This ensures that the material flows into every nook and cranny of the cavity, creating a precise and uniform preform shape.
Cooling and Solidification: After injection, the mold with the molten plastic is allowed to cool and solidify. Cooling time is carefully controlled to achieve optimal results.
Ejection: Once the preform has solidified, the mold is opened, and ejector pins push the preform out of the cavity.
Design Considerations for PET Plastic Preform Molds
Creating a successful PET plastic preform mold requires a thorough understanding of the product's design and manufacturing processes. Some crucial design considerations include:
Wall Thickness: The wall thickness of the preform must be uniform to ensure consistent quality and minimize defects during the blow molding process.
Gate Design: The gate is the entry point for the molten plastic into the mold cavity. Proper gate design is critical for ensuring minimal waste, smooth filling, and easy removal of the preform.
Cooling System: An efficient cooling system is essential to regulate the cooling process and maintain a consistent cycle time.
Ejection Mechanism: The ejection system must be designed to gently remove the preform from the mold without causing any damage.
TLDR
PET plastic preform molds are indispensable components in the production of PET bottles. The careful engineering and design considerations behind these molds ensure the creation of consistent and high-quality preforms. As technology continues to evolve, we can expect further innovations in PET plastic preform molding, resulting in more sustainable and efficient packaging solutions for a greener future.
Want to know more about the plastic injection molding process? Check out this video from Bill Hammack, Professor of Chemical and Bioelectrical Engineering at the University of Illinois.